Gears
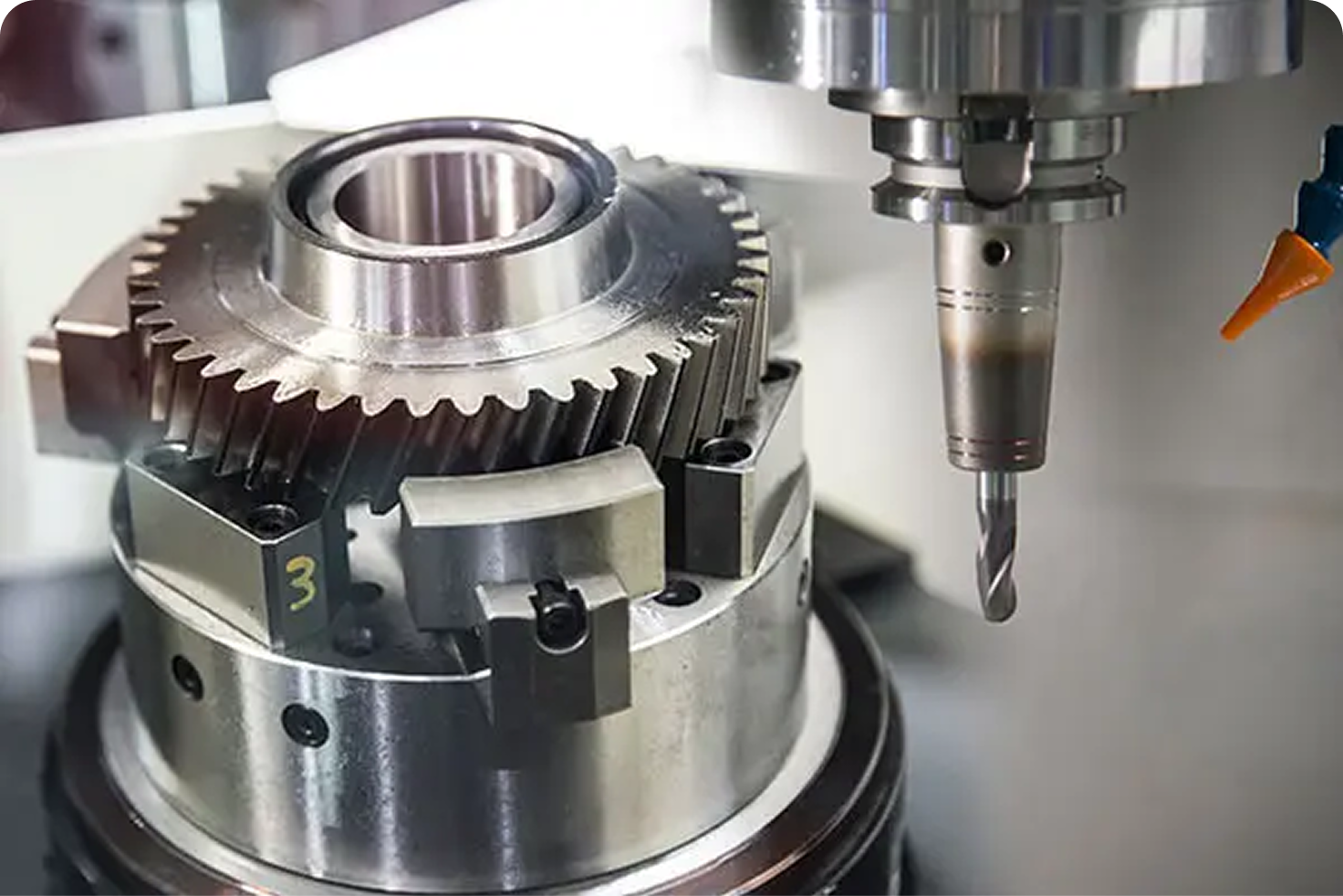
Custom Gear Manufacturing
AmTech International delivers fully customized gear solutions engineered for your unique application requirements. From initial design to final production, we combine advanced manufacturing techniques and rigorous quality control to ensure every gear meets your exact performance and durability standards.
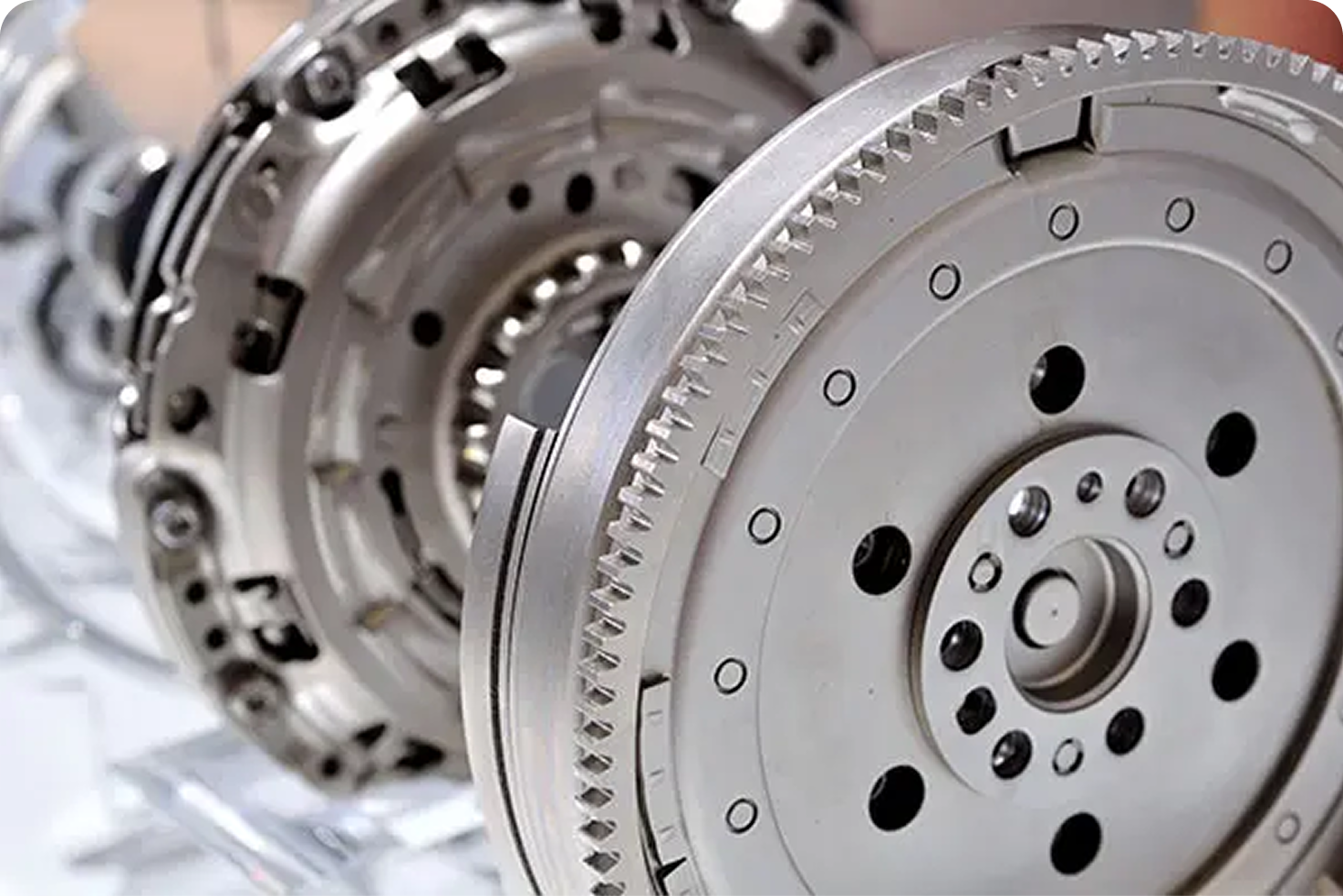
Flywheels – Single & Dual Mass
We offer both single and dual mass flywheels designed for a wide range of engine types. Our flywheels are engineered for maximum durability, optimal balance, and smooth operation, providing reliable solutions for both automotive and industrial powertrains.
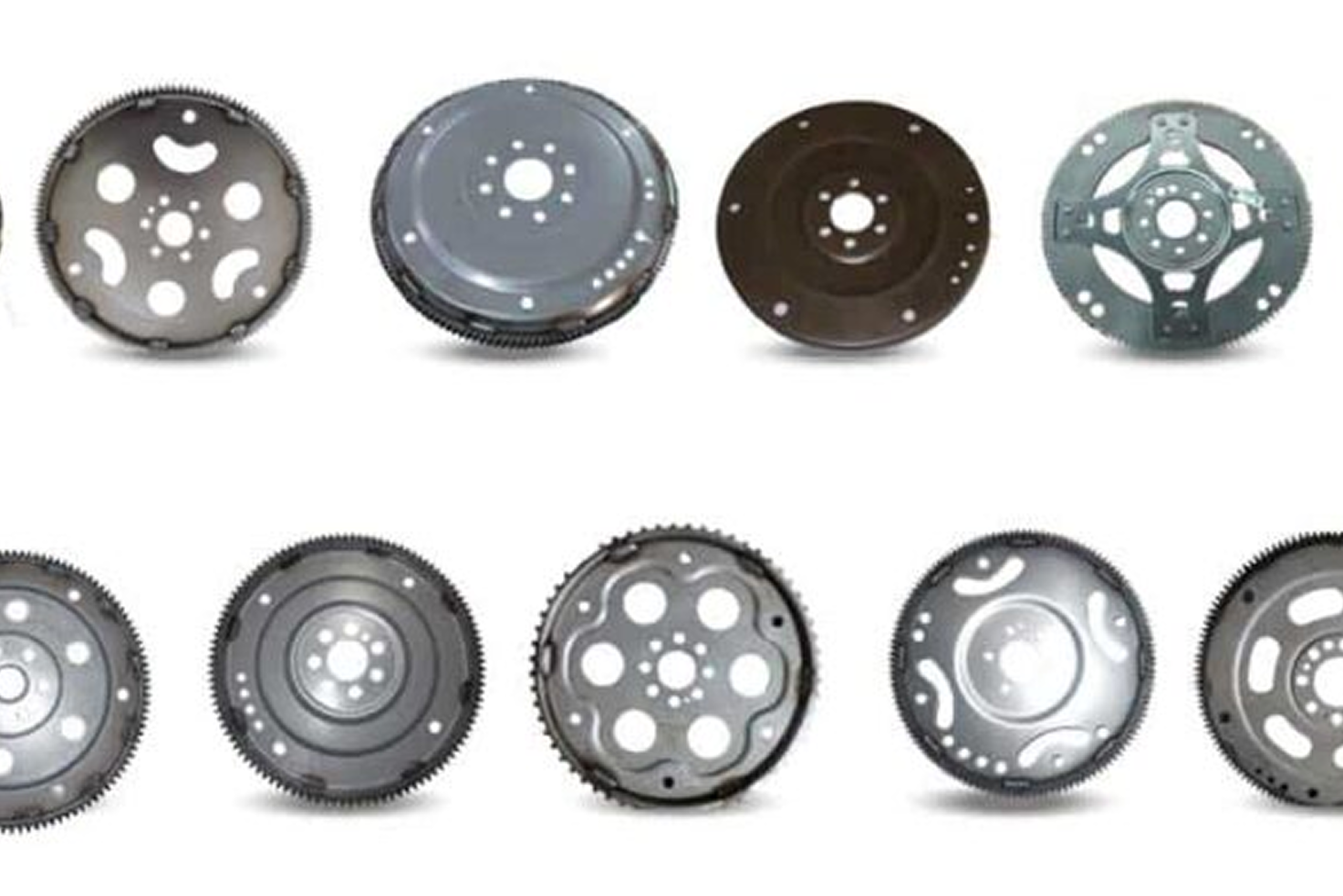
Flexplate Assemblies
As a trusted manufacturer of flexplate assemblies, AmTech ensures every product meets stringent quality standards. Our robust and reliable flexplates are ideal for automotive and industrial applications, delivering consistent performance under demanding conditions.
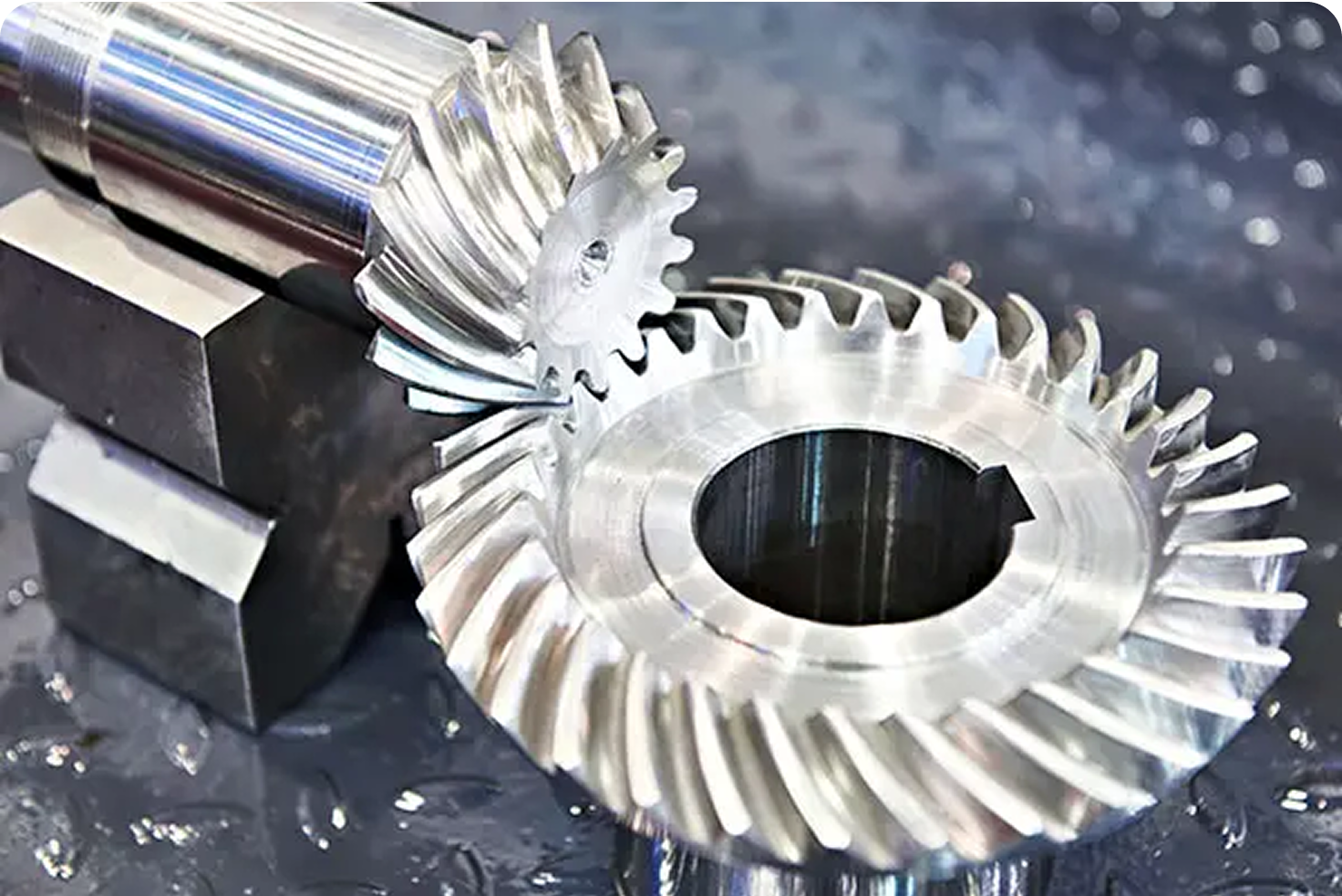
Bevel Gears
Our bevel gears are expertly crafted for smooth, efficient angular motion and power transmission. Designed for high torque and operational reliability, these gears are suitable for a variety of mechanical systems requiring precise directional changes.
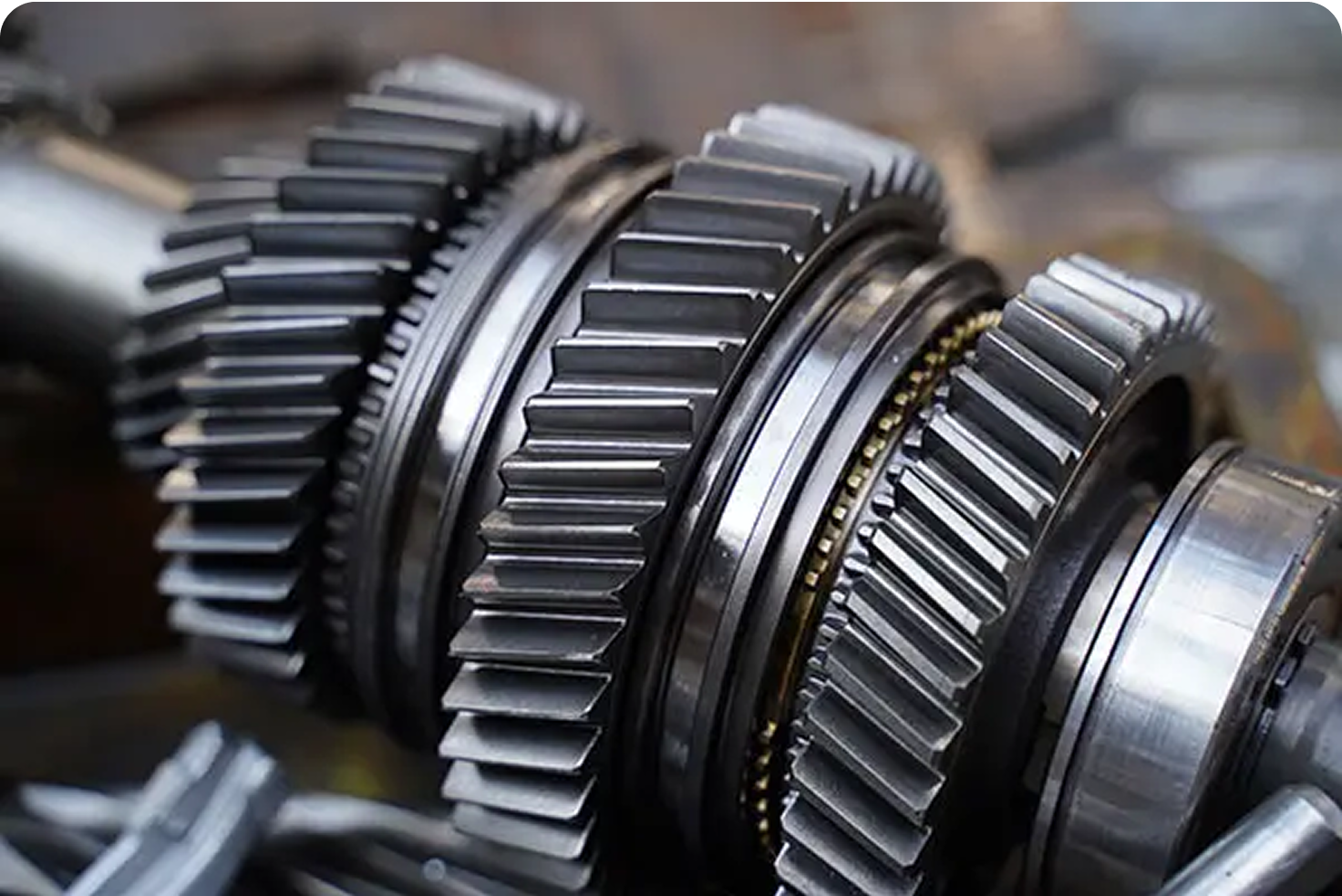
Helical Gears
AmTech’s helical gears are known for their quiet operation and high load-bearing capacity. Engineered for smooth and efficient power transmission, they are ideal for applications where noise reduction and performance are critical.
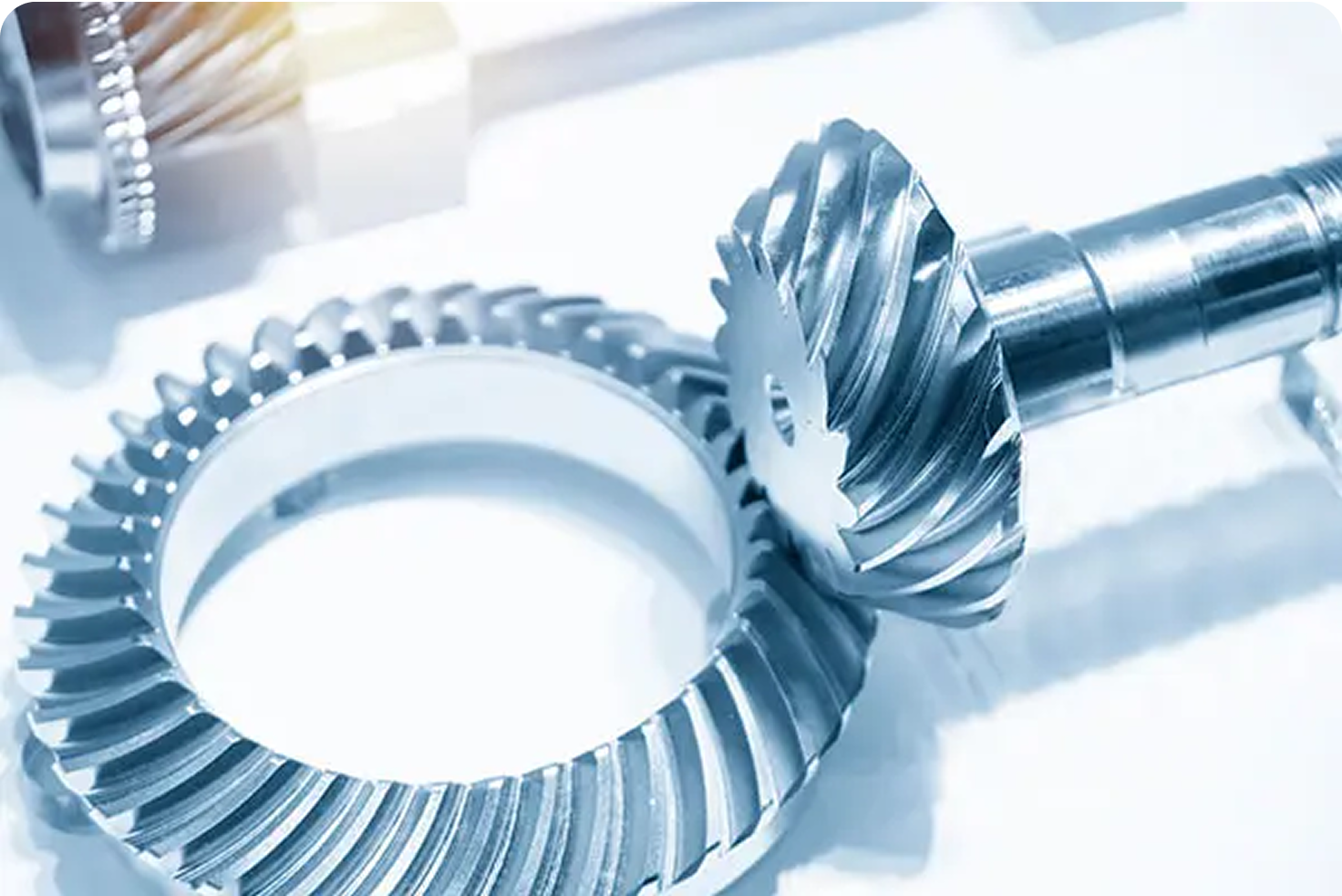
Ring & Pinion Gears
We supply precision ring and pinion gear sets that deliver optimal gear ratios for efficient power transfer in drivetrains. Our products are recognized for their durability, accuracy, and long service life in automotive and industrial applications.
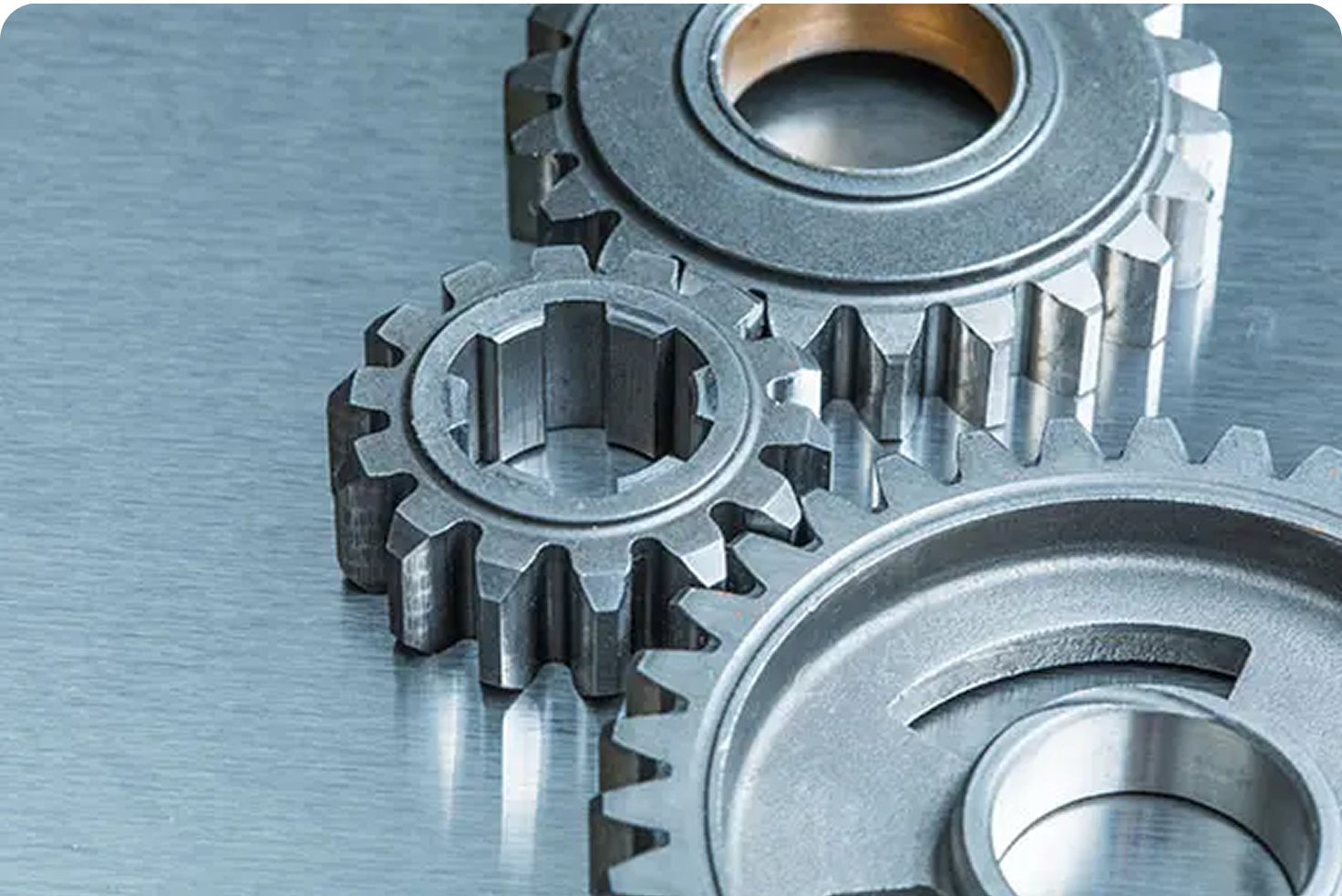
Spur Gears
Our spur gears are designed for effective power transmission with minimal noise. Ideal for a wide range of machinery, they are valued for their strength, reliability, and precise alignment.
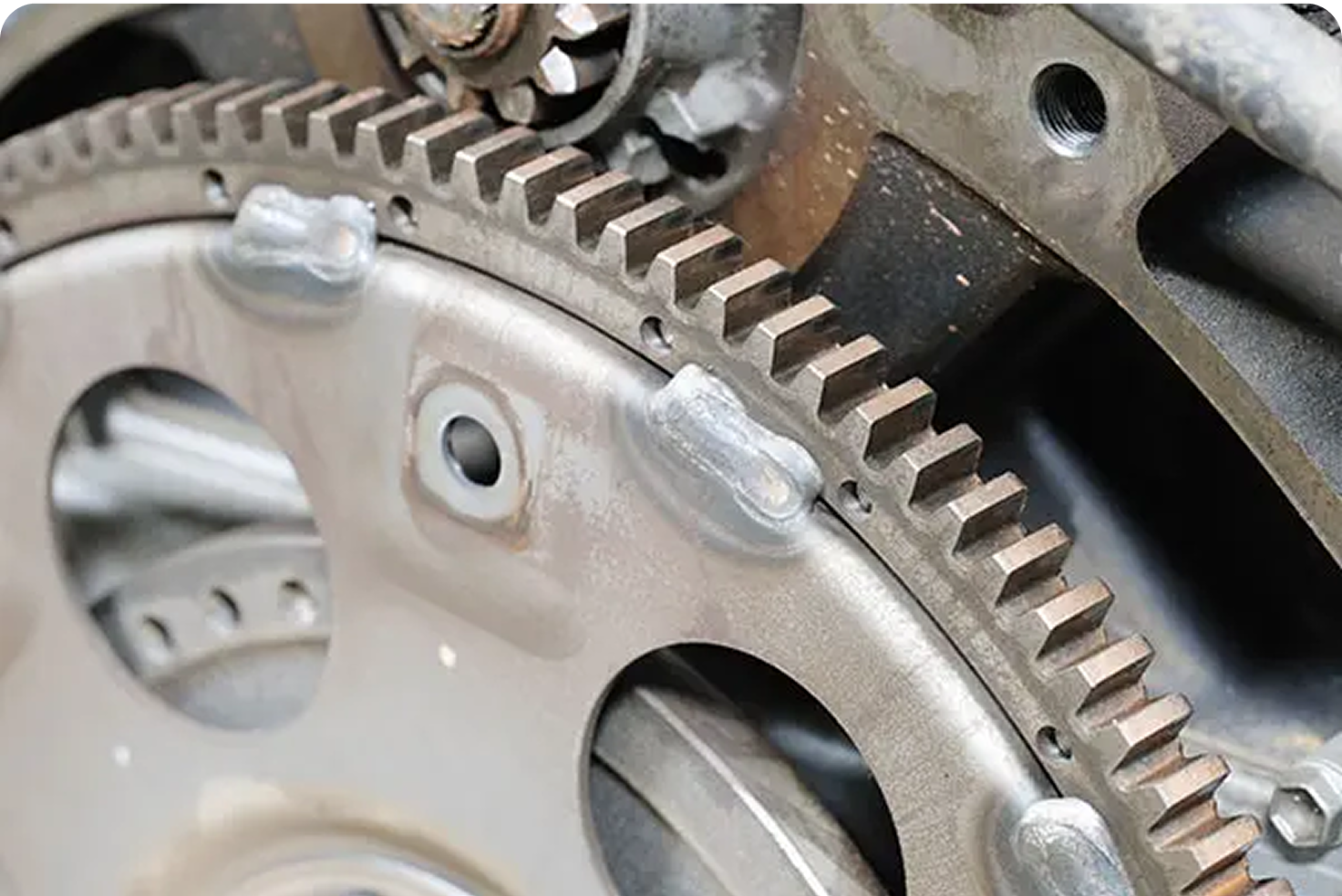
Starter Ring Gears
We manufacture robust starter ring gears engineered for reliable engine starting. Built to withstand high torque and repeated use, our gears ensure dependable performance and extended longevity.
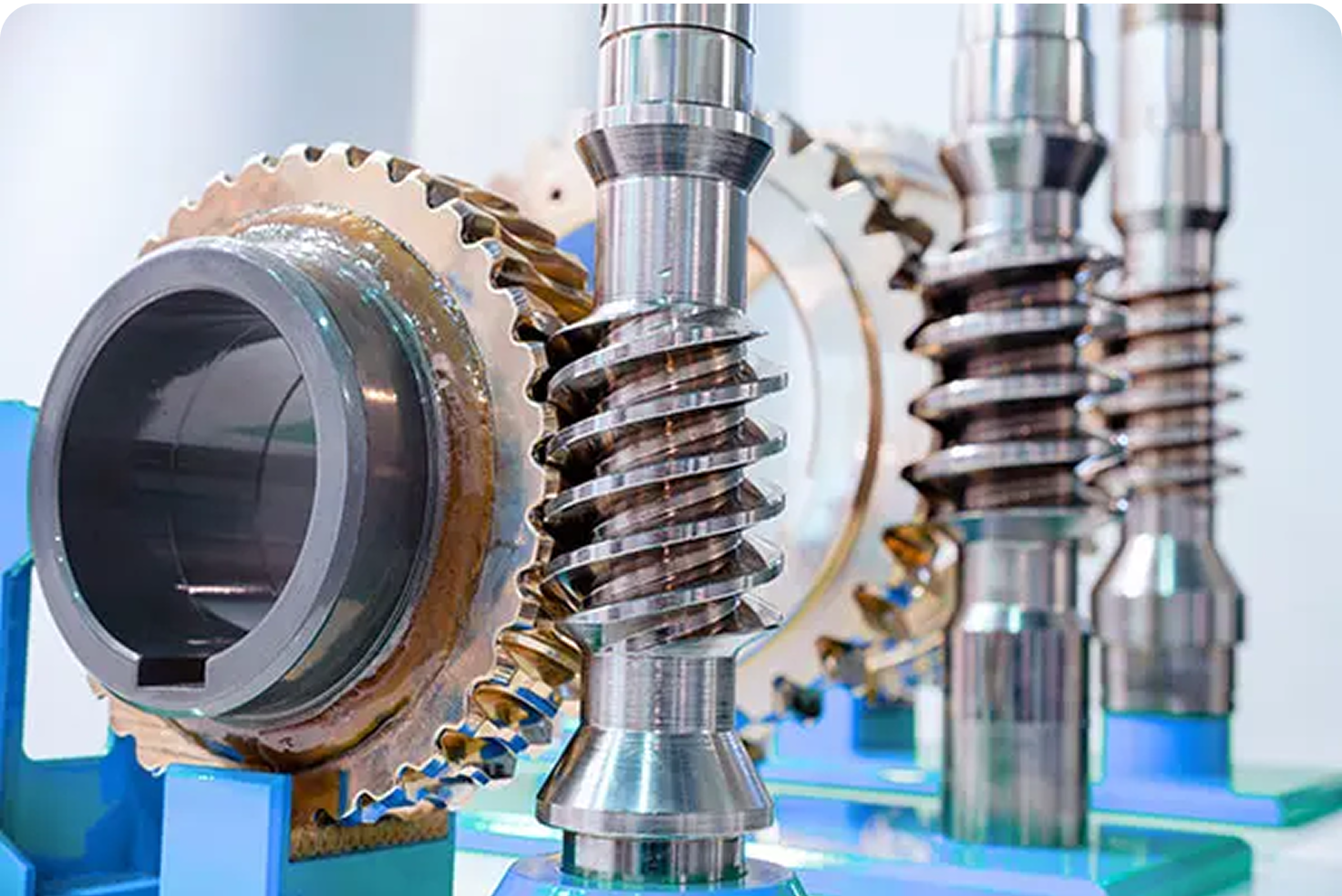
Worm Gears
Specializing in worm gears, we offer solutions for applications requiring significant torque reduction and smooth, quiet operation. Our worm gears are known for their efficiency, precision, and durability in heavy-duty environments.
FAQ's
Frequently Asked Questions
What types of gears does AmTech International manufacture?
Can you manufacture gears to my exact specifications?
What industries use your custom gears and assemblies?
What are the benefits of single vs. dual mass flywheels?
How do you ensure the quality and consistency of your gears?
All gears are produced in ISO 9001, IATF 16949, and QS 9000 certified facilities and undergo rigorous inspection and testing for dimensional accuracy, strength, and surface finish.
Can you assist with gear design and engineering?
Absolutely. Our engineering team works closely with clients to optimize gear geometry, materials, and manufacturing processes for best performance and cost efficiency.
Do you offer prototyping and rapid sampling for new gear projects?
How quickly can I get a quote for custom gears or assemblies?
We typically provide detailed quotes within 7–10 business days. Submit your requirements through our Request a Quote form or contact us for prompt assistance.