Machined Casting
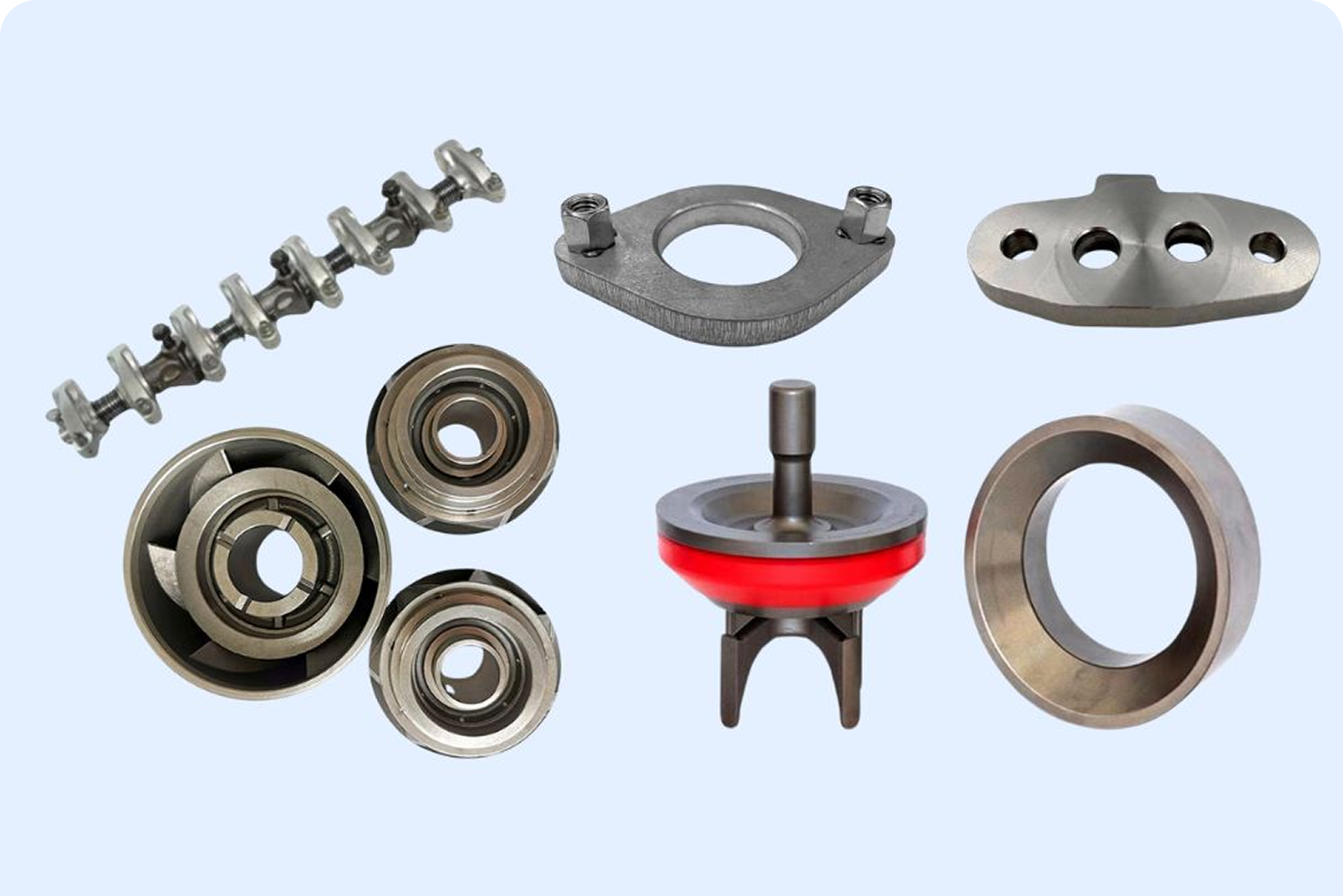
Investment Casting
AmTech offers investment castings with intricate details and complex geometries, suitable for high-precision, alloy-specific parts with excellent surface finishes and minimal machining required.
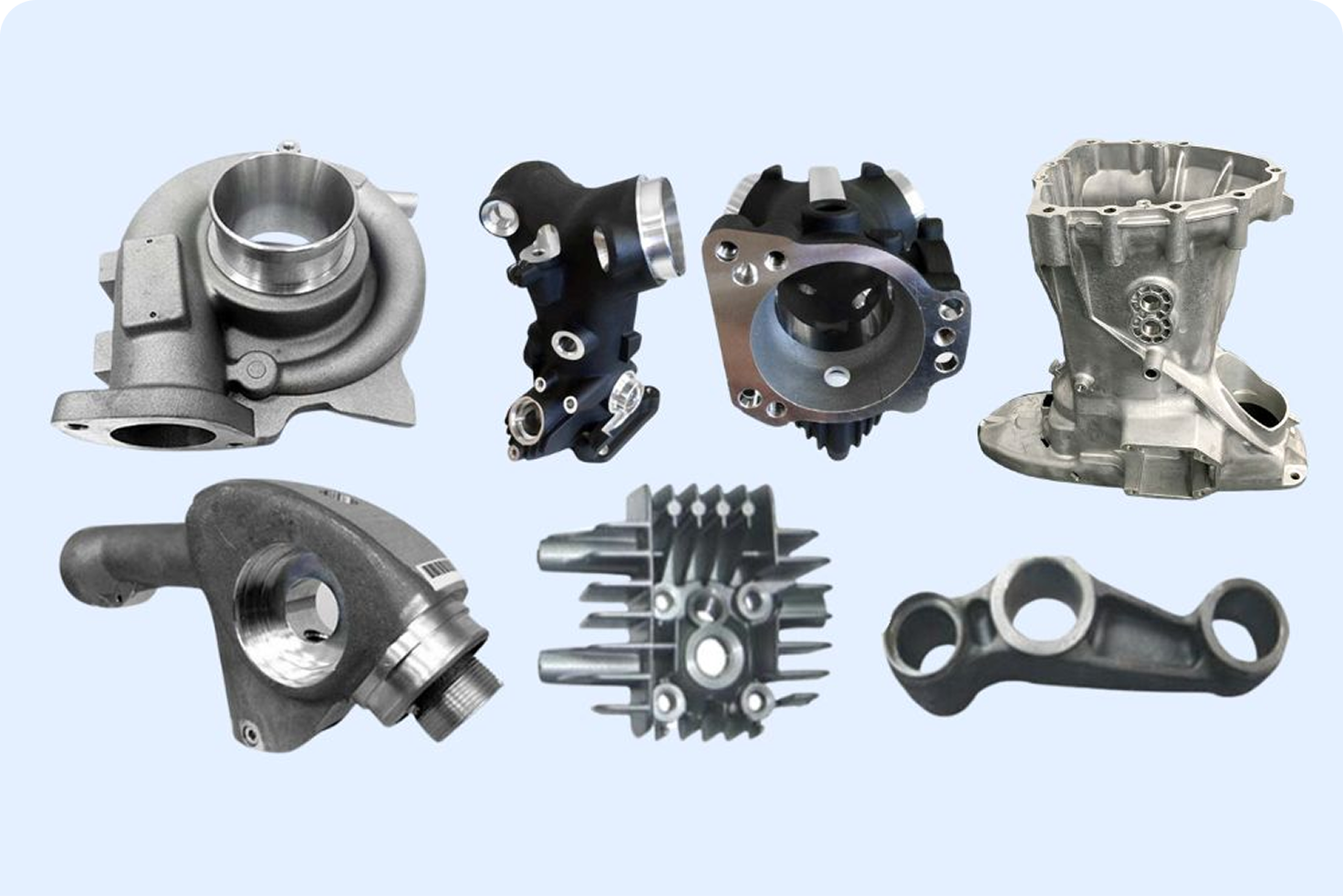
Gravity Casting
The Gravity Casting process is a cost-effective alternative to sand casting that can be utilized to create a variety of parts in different sizes using aluminum and other light alloys.
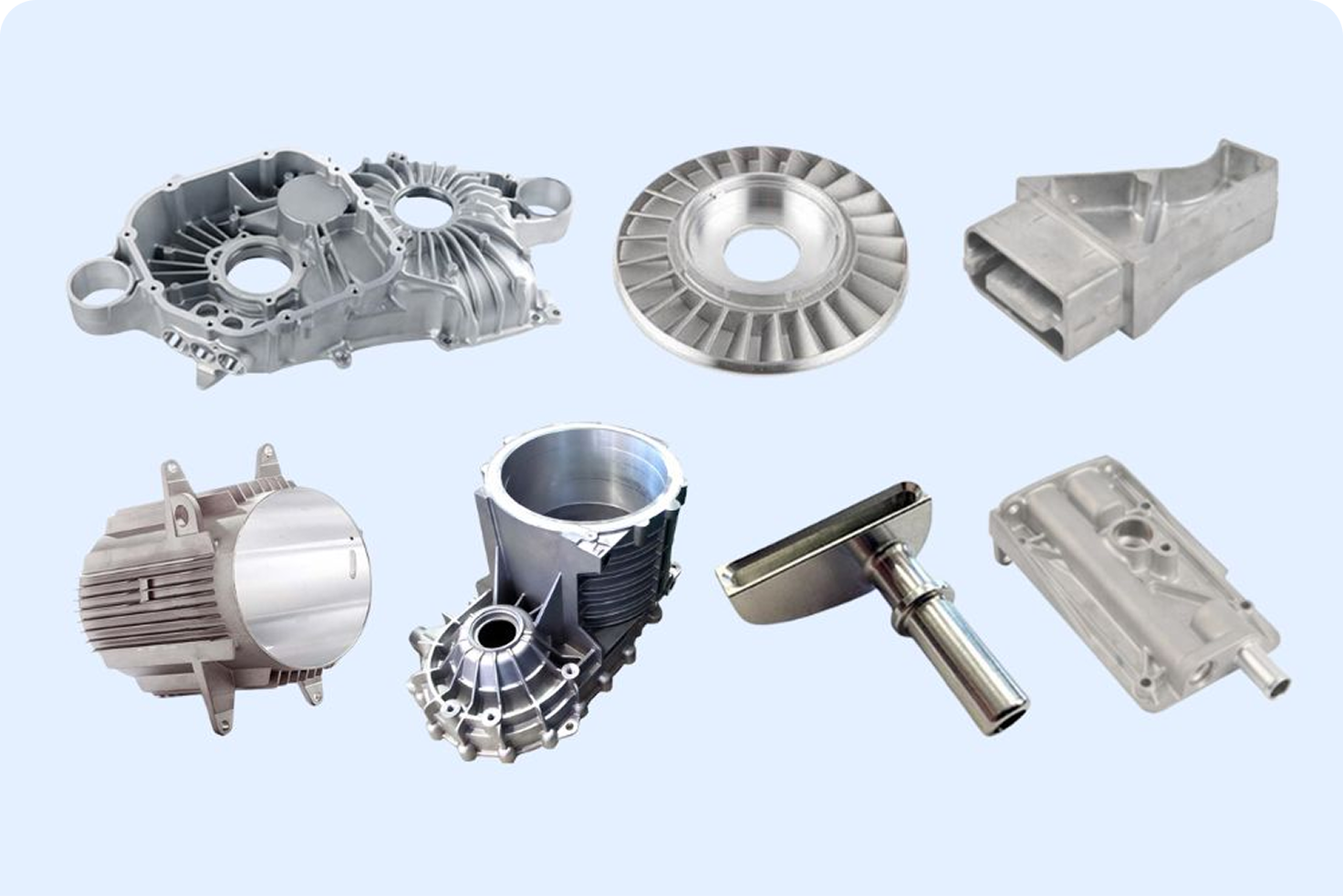
Die Casting
Die casting is ideal for large-scale production runs. It's a cost-effective process for producing aluminum and other metal products, including zinc and magnesium.
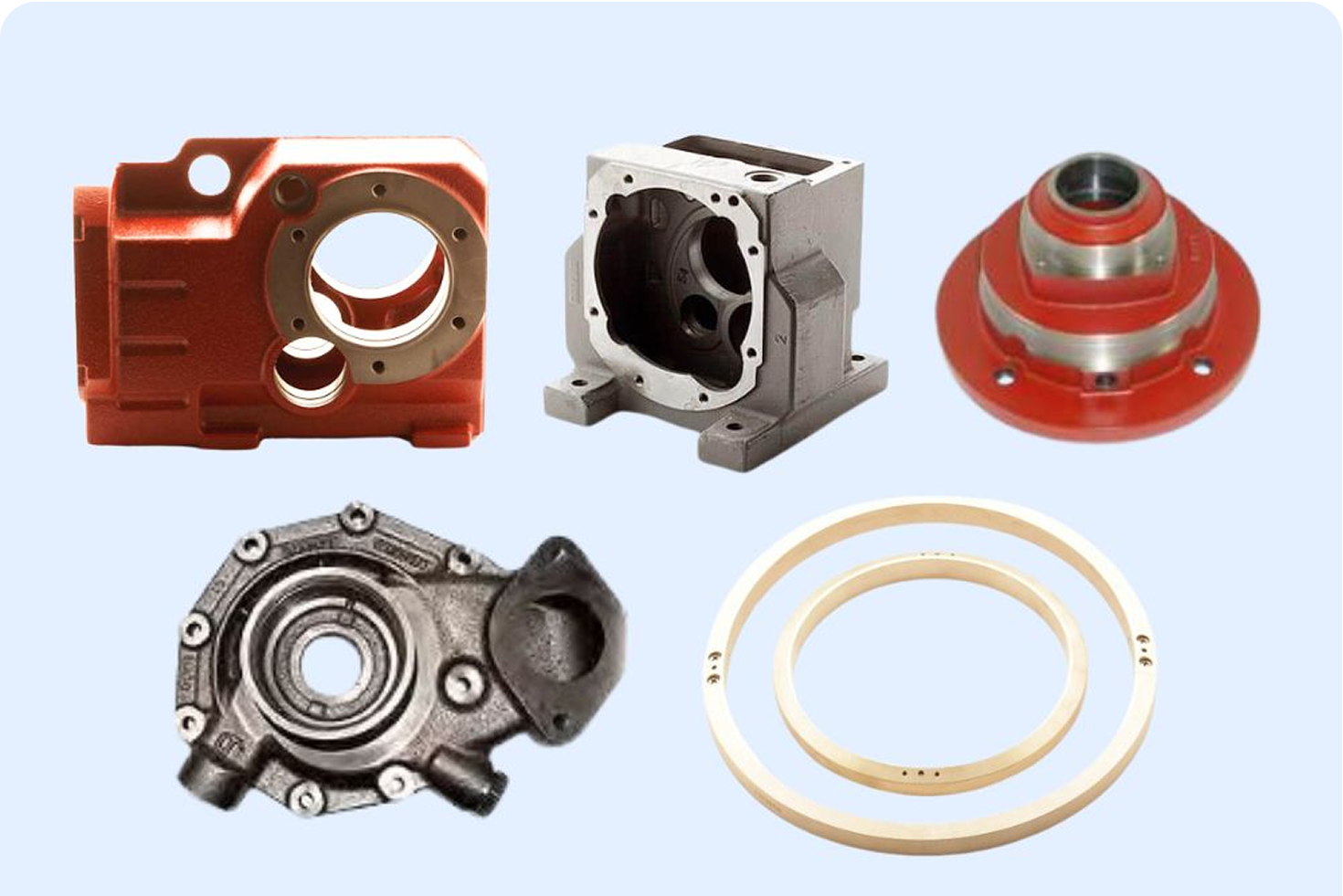
Sand Casting
AmTech’s sand casting process produces high-quality metal components in a wide range of sizes and materials, including aluminum, iron, and steel.
FAQ's
Frequently Asked Questions
What types of machined casting processes does AmTech offer?
What materials can be used for machined castings?
How do I choose the right casting process for my project?
The best process depends on your part’s geometry, size, material, surface finish, and production volume. Contact us for expert guidance on selecting the most cost-effective and efficient method.
What industries use AmTech’s machined castings?
What are the advantages of investment casting?
When is gravity casting a good alternative to sand casting?
Can AmTech support both sampling and mass production?
How do I request a quote or get started with a machined casting project?
Simply request a quote or contact us with your project details, and our team will review your requirements and provide a tailored proposal.