Custom Shaft Manufacturing
Comparing Material Choices for Custom Shaft Manufacturing
If you design mechanisms that use shafts, how much thought do you give to the shafts themselves? You probably consider loads, dimensions, and features like gears, but how much time is spent exploring material options? The material you choose for your shaft makes a great deal of difference, as each material has unique properties that impact the overall function and form of the shaft.
The Application Guides Material Choice
Generally, shaft applications require three primary characteristics: strength, stiffness, and fatigue resistance. These properties are needed because shafts transmit rotational forces and are subject to torsional forces and often side loads resulting from forces imposed by the application. In some cases, there may also be acceleration and deceleration loads to consider.
Some applications may require corrosion resistance, especially if the shafts are being used in marine environments.
Additionally, the chosen material influences the manufacturing processes used. So, switching from one material to another might reduce manufacturing costs, but at the expense of some design changes.
Let’s look at some of the most common material choices used in shaft manufacturing.
Shaft Material Choices
Brass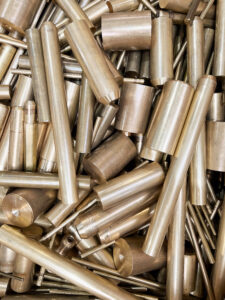
Brass, technically a copper-zinc alloy, has a long history of use in custom shaft manufacturing. Depending on its composition, its yield strength ranges from 18 to 45K PSI, and its UTS is between 49 and 68K PSI.
Brass has an attractive yellow hue and is naturally corrosion-resistant. It also has antimicrobial properties, which may be beneficial in some applications. Its machinability is excellent, making it feasible to produce complex forms and profiles. Brass is often used as shaft material in precision-engineered applications like timepieces and measuring instruments.
Carbon Steel
“Carbon steel” is a catch-all term that can refer to low, medium, or high carbon steel. Hardness increases significantly at higher levels. Low and medium carbon steels (carbon content in the 0.25 to 0.6% range) generally have good toughness, often making them the better choice for shafts.
The yield strength of low carbon steel is 45 to 58K PSI, and the ultimate tensile strength (UTS) is 53 to 69K PSI. For medium carbon steels, the ranges are 64 to 80K PSI and 76 to 118K PSI, respectively. In terms of strength per dollar, the medium carbon steels are often of very good value.
High carbon steel, with carbon content between 0.6 and 1.5%, are generally classed as alloy steels. These steels have higher hardness and excellent wear resistance.
Stainless Steel
Stainless steel contains more than 10% chromium, which increases hardness, strength, and corrosion resistance. For shafts, two preferred types of stainless are 303 and 304. Both grades are austenitic/non-magnetic and incorporate around 18% chromium. Corrosion resistance of both grades is good, although 304 rates higher, making it the better option for marine applications.
303 is suitable for hot forging but not cold working. 304 is the more weldable of the two and is also available in low and high carbon grades.
At 60K PSI, the yield strength of 303 stainless is almost double that of 304. However, for both, UTS is around 90K PSI.
Hot Rolled & Cold Rolled Steel
Rolling is the process of forming thick billets into smaller section bars. This process can be done in two ways: with the steel heated to over 1,700 degrees Fahrenheit or at ambient temperature. Hot rolling requires lower forces, so it’s typically faster and less expensive. However, it results in a gray, scaly finish and significant dimensional variation.
In contrast, cold rolling requires more force but leaves a smoother surface and is more accurate. Cold rolled steel is also stronger than hot rolled, with a yield strength of 70K PSI and a UTS of 85K PSI.
Aluminum
Lastly, while aluminum is rarely the first choice of material for shaft manufacturing, its properties are ideal for some applications. First, it has a high specific strength, so it’s worth considering if the application will benefit from mass reduction. It’s also corrosion-resistant and an excellent heat conductor.
Aluminum alloys are grouped into seven series, each with a different composition and properties. The “workhorse” grade is 6061 T6, (T6 refers to the temper), which has a yield strength of 35K PSI and UTS of 42K PSI.
When higher strength is needed, the 7xxx series “aerospace-grade” aluminum alloys may be the answer. In particular, the strength of 7075 aluminum approaches that of steel.
Learn More From AmTech
AmTech uses processes like forging, investment casting, and precision machining to manufacture screw machine parts, fasteners, gears, and custom shafts for Tier I & Tier II suppliers in industries from automotive to industrial equipment.
Visit our blog for more manufacturing resources, or contact us today to learn more about our capabilities.