Shafts
We provide a full range of precision gears, including flywheels, flexplate assemblies, bevel gears, helical gears, ring & pinion sets, spur gears, starter ring gears, and worm gears.
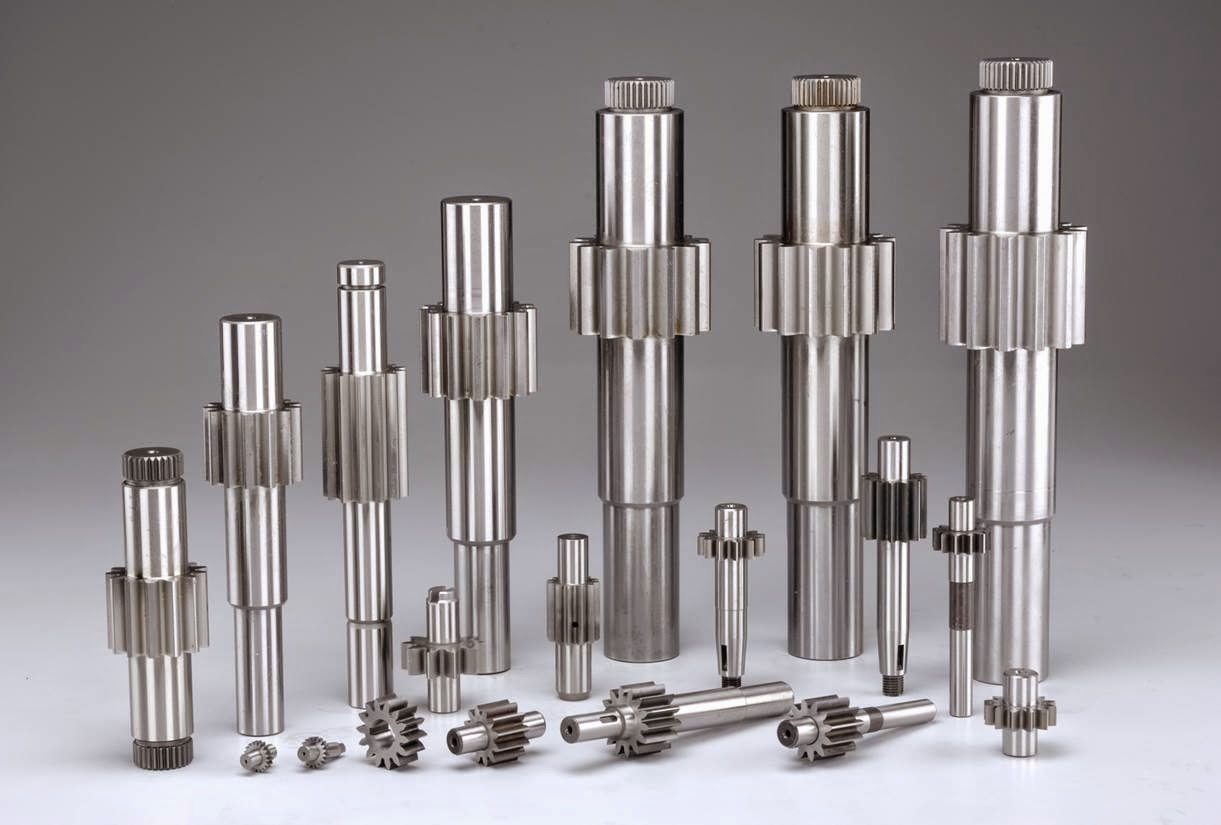
Specializing in precision-engineered shafts, our process ensures high-quality results. Tailored to client specifications, each shaft is crafted with utmost care and precision.
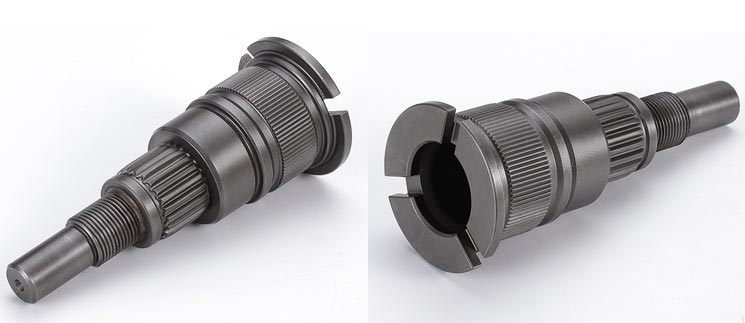
Utilizing advanced forging techniques, these shafts boast superior strength and durability. Ideal for heavy-duty applications, each shaft is meticulously shaped and refined.
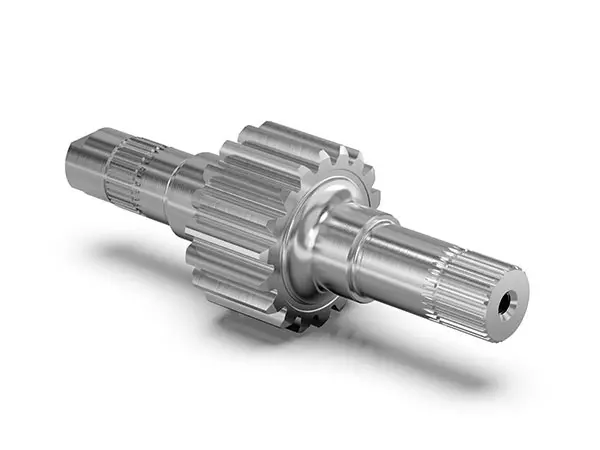
Expertly designed for gear systems, these shafts are crafted for seamless integration and optimal performance. Precision engineering guarantees consistent quality and reliability.
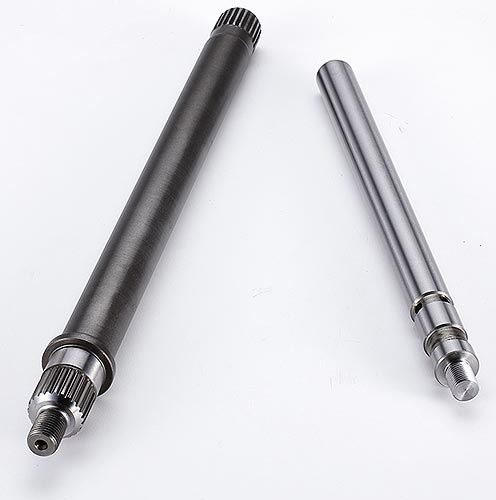
Offering straightforward solutions for motor shaft manufacturing, these shafts are produced with efficiency and precision. Perfect for standard motor applications, providing reliability and quality.
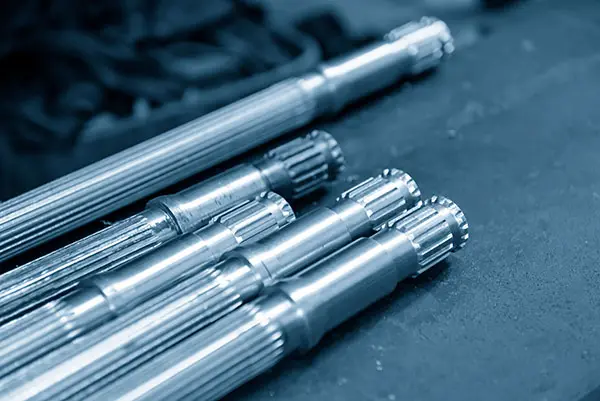
Incorporating intricate spline designs, these shafts are tailored for complex mechanical systems. Precision and attention to detail ensure a perfect fit and exceptional performance.

Employing state-of-the-art laser welding, these shafts combine different materials for enhanced functionality. Each shaft is carefully welded for strength and versatility.
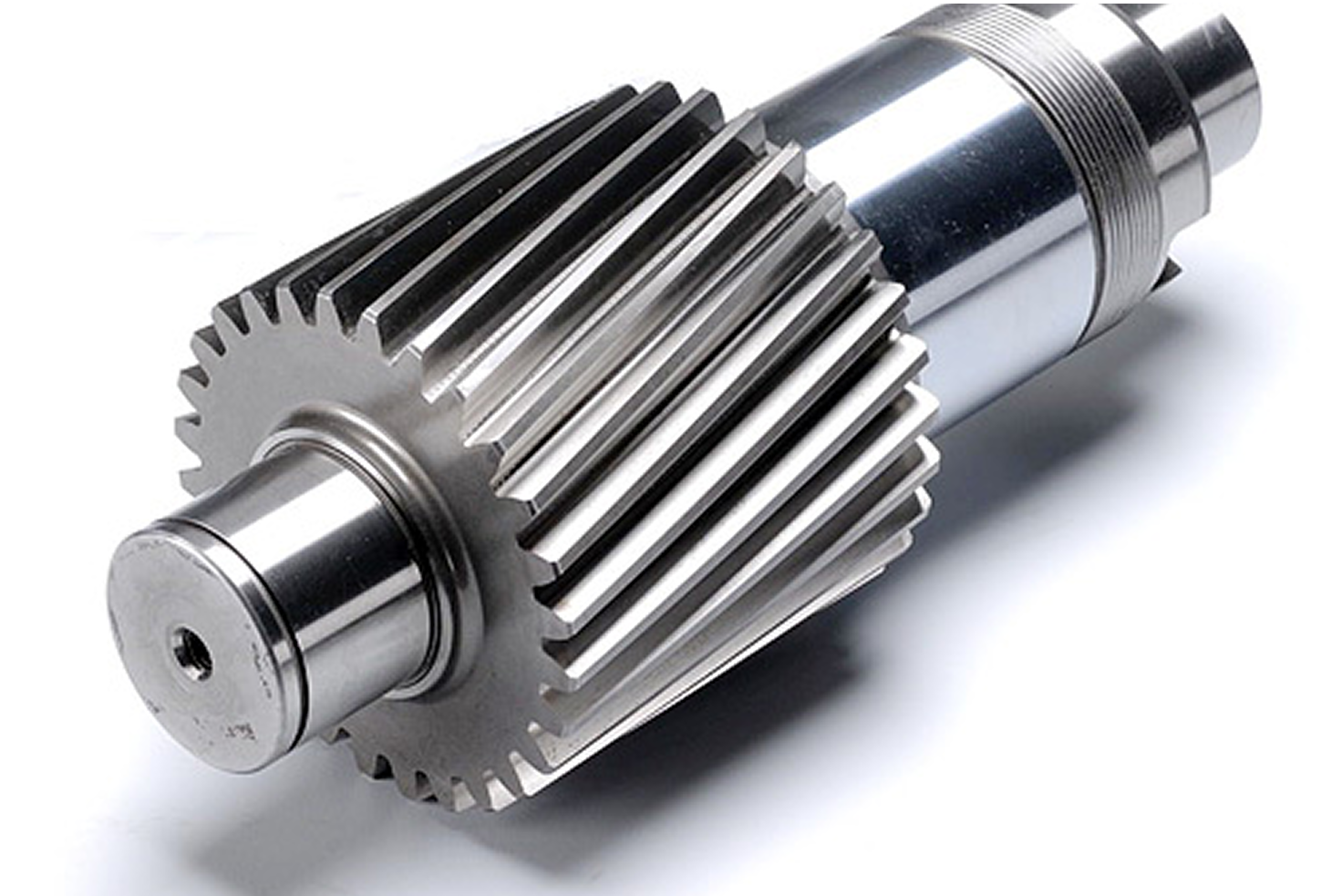
Specializing in precision-engineered shafts, our process ensures high-quality results. Tailored to client specifications, each shaft is crafted with utmost care and precision.
FAQ's
Frequently Asked Questions
What types of shafts does AmTech International manufacture?
Can you manufacture shafts to custom specifications?
What materials are available for shaft manufacturing?
What industries use your precision shafts?
What is the difference between forged, welded, and machined shafts?
Do you offer prototyping and engineering support for new shaft designs?
How do you ensure the quality and reliability of your shafts?
How can I request a quote or start a shaft project with AmTech International?
Simply contact us or fill out our Request a Quote form. Our team will review your requirements and provide a detailed proposal and timeline.