Additional Services
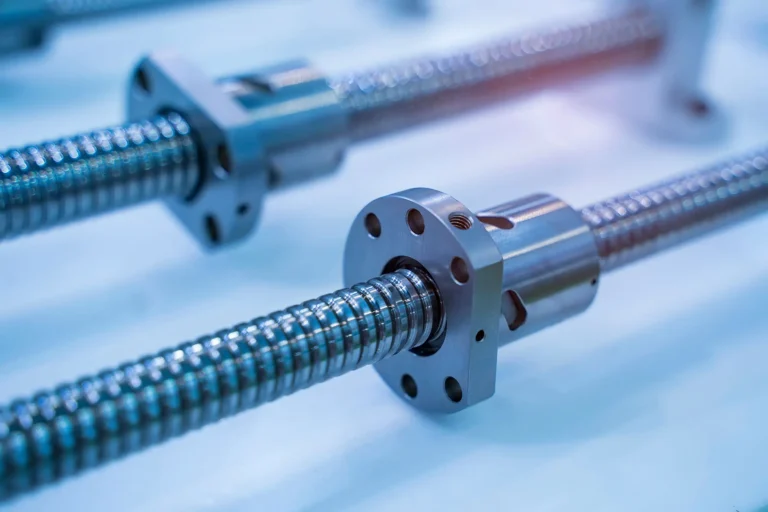
Shafts
AmTech offers a broad assortment of shafts for automakers, industrial machinery, and other applications. Our capabilities extend from gear shafts to multi-section laser-welded shafts.
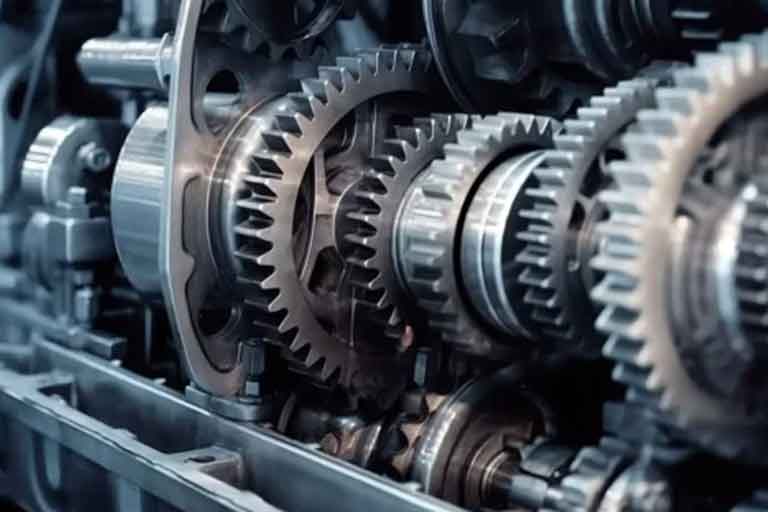
Gears
Our gears are precision-ground and cut to meet the demands of any industrial application. Contact us for assistance with parts such as Flywheels, Flexplate Assemblies, Starter Ring Gears, and more.
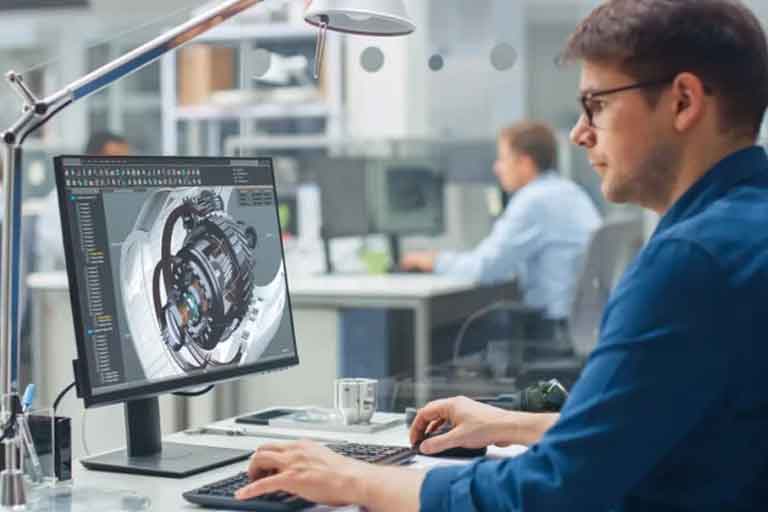
Prototyping & Engineering
AmTech's experienced engineering team has the expertise to assist with even the most custom and intricate designs. After completing the design, we'll manufacture a prototype using advanced processes.
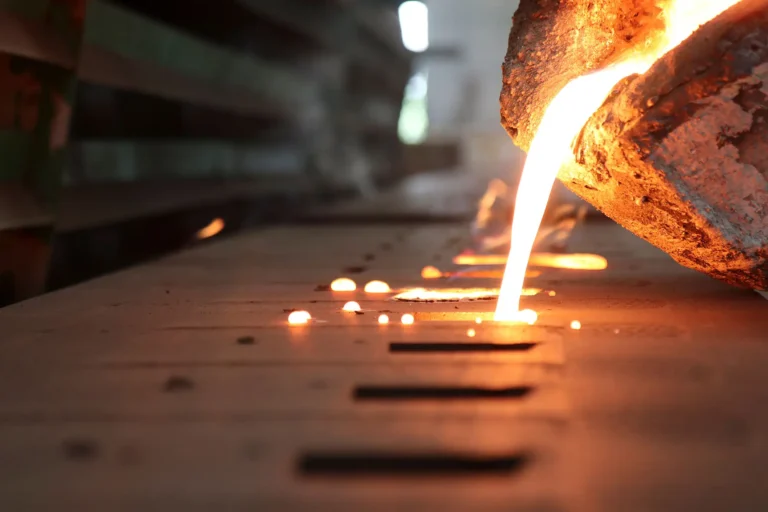
Gravity Castings
The Gravity Casting process is a cost-effective alternative to sand casting that can be utilized to create a variety of parts in different sizes using aluminum and other light alloys.
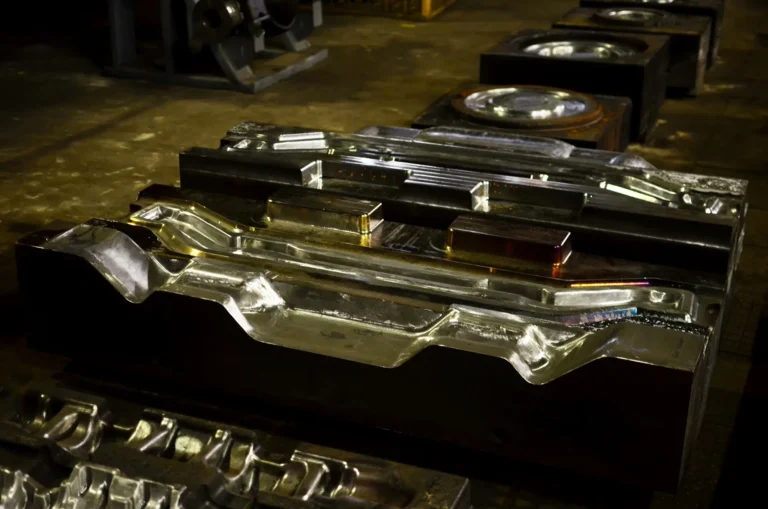
Die Casting
Die casting is ideal for large-scale production runs. It's a cost-effective process for producing aluminum and other metal products, including zinc and magnesium.
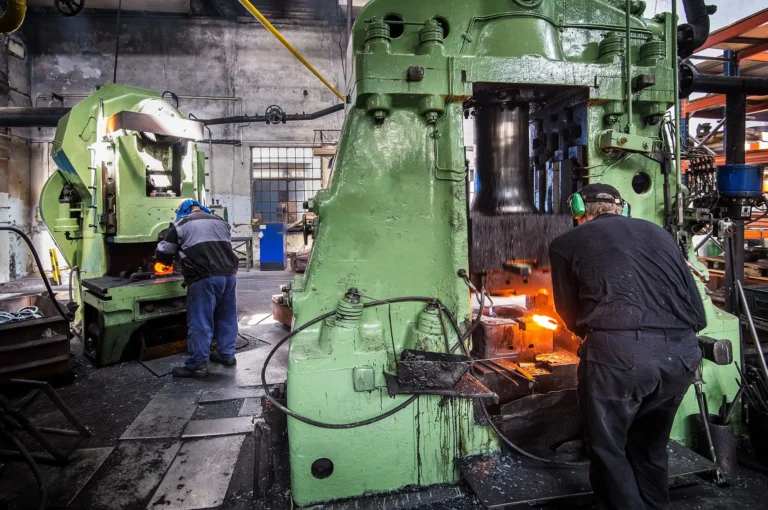
Forging
AmTech OEM's forged component division specializes in precision-machined forging. To determine the best forging process for your project, contact us today.
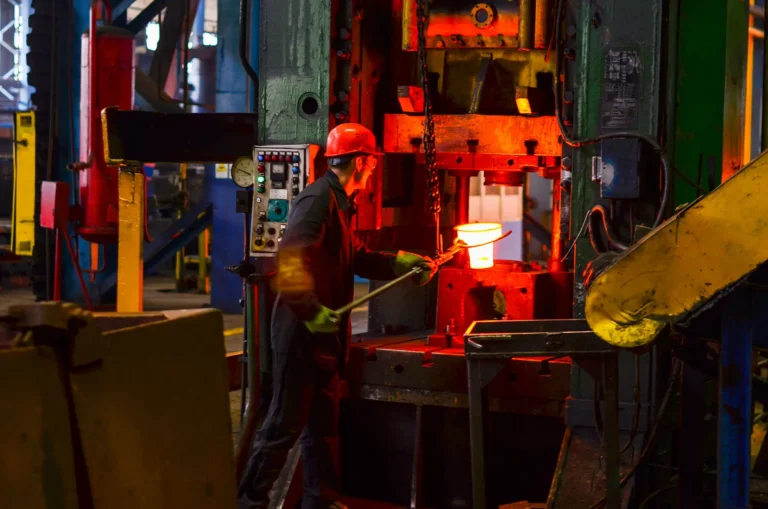
Hot Forging
Utilize hot forging for your project to add a layer of uniformity and durability to the finished product, and is an ideal process for steel and certain types of alloys.
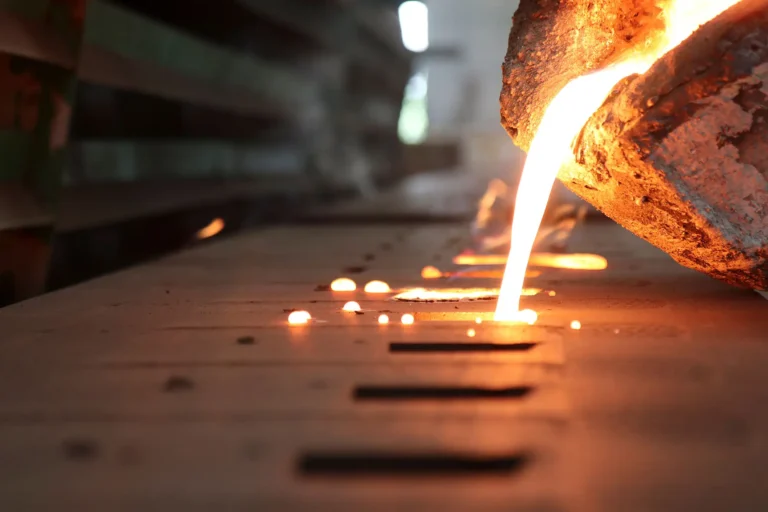
Sand Castings
The Gravity Casting process is a cost-effective alternative to sand casting that can be utilized to create a variety of parts in different sizes using aluminum and other light alloys.