Investment Casting
Stainless Steel Casting Versus Aluminum Casting
Casting is a highly regarded manufacturing process because it can produce complex, near-net shape parts with fine details that require little machining.
Any ferrous or nonferrous metal can be cast, but two of the most widely used are stainless steel and aluminum. Although they look similar superficially, their properties are very different. In this blog, we’ll review their characteristics, advantages and disadvantages, and factors to consider when choosing between the two.
Stainless Steel
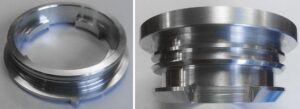
Like all steel alloys, stainless steel is primarily iron, with its carbon concentration reduced to around 0.1%. (Cast iron contains 2 to 5% carbon.) However, stainless differs from standard iron in chromium concentration, which is at least 10.5%. This concentration gives it high tensile strength and excellent corrosion resistance because surface chromium quickly oxidizes to form a protective layer that prevents rusting.
Unlike many other metals, stainless steel retains useful levels of strength at elevated temperatures and is often used in high-temperature environments (900 degrees Fahrenheit or higher).
Good methods for casting stainless steel are sand casting and investment casting. Die casting is impractical due to the high temperature at which the metal is poured.
Primary Advantages & Disadvantages
Some grades of stainless steel are difficult to weld, and most present some machinability challenges due to their high hardness. This makes stainless steel casting attractive, as it enables the production of complex shapes and minimizes the need for machining and welding.
A further advantage of casting stainless steel is that the produced parts don’t need painting, plating, or powder coating to protect against corrosion.
Disadvantages are application-specific. Stainless steel castings, while hard and strong, are also heavy, which is often a limitation in transportation-related applications.
Common Applications
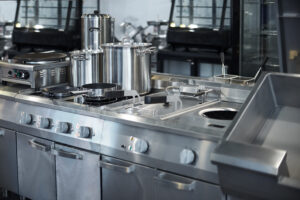
Stainless steel is often the material of choice when castings are used in corrosive environments, subjected to aggressive cleaning and sterilization regimens, and/or when the application requires high strength.
Examples include:
- Chemical processing equipment
- Food and beverage production machinery
- Medical devices
- Engine components (gas turbines as well as gasoline and diesel)
- Power transmission components (gears, shafts, etc.)
- Architectural elements (handrails, handles, columns, and posts)
- Components for use on boats and ships
- Material handling systems
Common Grades Used in Casting
Stainless steel alloys are produced in a wide range of compositions. The most widely used are:
- 304: Also called CF-8 in the Alloy Casting Institute system.
- 316: Also called CF-8M, this is more corrosion-resistant than 304.
- 410: Strong, but lower corrosion resistance.
- 17-4 PH: The strongest grade of stainless steel. It has good corrosion resistance.
Note that an “L” suffix in a grade means reduced carbon content, which improves weldability.
Aluminum
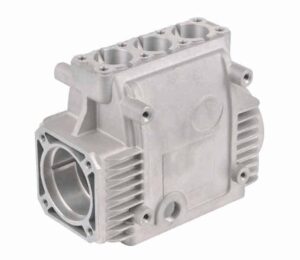
Freshly cut aluminum has a bright, silvery appearance but quickly dulls as the exposed surface oxidizes. However, like stainless steel, oxidation protects the metal against further corrosion, so it doesn’t rust.
Aluminum is lightweight and, in its pure form, very soft. Alloying with other elements, such as silicon, is essential to raising its strength to a useful level. Its melting point is around 1,050 degrees Fahrenheit, and the maximum working temperature limit is around 400 degrees Fahrenheit. Additionally, its thermal and electrical conductivity are comparable to copper’s.
Most aluminum alloys have good machinability because their hardness is relatively low. Their ductility is better than that of many ferrous metals. When casting aluminum, sand, investment, and die-casting processes are all practical options, making it an extremely versatile material choice.
Primary Advantages & Disadvantages
The primary advantages of aluminum are its corrosion resistance, high strength-to-weight ratio, and heat conductivity.
However, although aluminum does have enough corrosion resistance, it may still need coating if the casted part is expected to operate well in very corrosive environments.
Common Applications
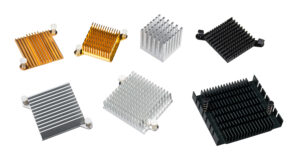
Aluminum is often used when low mass is part of the design criteria and/or when heat needs to be conducted between two points.
Common applications include:
- Automotive components
- Appliances
- Small engines
- Decorative items
- Heat sinks
- Aircraft components (cabins, landing gear, and airframes)
- Beverage containers
- Cookware
Common Grades Used in Casting
The various types of aluminum alloy are defined in terms of series. Series numbers range from 1000 to 7000 series. The most widely used are:
- 3000: Used in cookware and beverage cans.
- 5000: Used when corrosion resistance is a priority, as in construction and marine applications.
- 6000: The ‘workhorse’ grade, which provides a combination of low mass, good strength, corrosion resistance, and weldability.
- 7000: The high-strength ‘aerospace’ grades, which can be challenging to machine and weld.
Considerations When Choosing
Application Requirements
The primary consideration is application requirements.
For the highest strength and corrosion resistance, stainless steel wins every time. It’s also best for high-temperature applications.
But, when low mass or thermal conductivity is required, as in transportation or heat sink applications, the equation shifts.
For example, aluminum’s high strength-to-weight ratio means it may be possible to achieve an application’s strength goals by increasing the size of the casting. Additionally, although aluminum has lower corrosion resistance than stainless steel, aluminum may still be a good enough option over stainless steel if the part is being used in a dry indoor environment.
Cost
Cost is always a consideration in alloy selection. For the two metals discussed here, the final part cost is a function of the metal itself and the manufacturing processes.
Of the two, aluminum is less expensive than stainless steel. Both are suitable for investment casting, a cost-effective production process for making complex parts that require minimal machining.
Tooling
A further consideration is tooling lead time and cost. Investment casting uses wax patterns, which themselves need tooling. Tooling lead times are shorter and costs lower for sand casting, but the parts will need more post-process machining. Thus part complexity is a significant factor in selecting a casting process and even an alloy.
Learn More About Investment Casting From AmTech
Founded in 1995, AmTech is a specialty Tier 1 & Tier II manufacturer offering a wide range of capabilities, including die, gravity, investment casting, and prototyping. We proudly serve businesses worldwide in many industries, from automotive and construction to medical.
Please visit our blog for more casting resources or contact us today to learn more about what we can do for you.